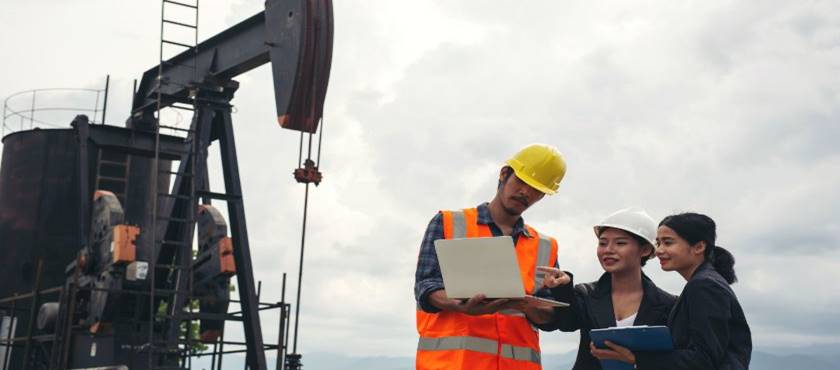
Equipment Troubleshooting
Equipment troubleshooting and root cause analysis are critical components of maintenance and engineering consultancy solutions. These processes help identify and resolve underlying issues that cause equipment failures, ensuring reliable and efficient operations. Troubleshooting involves systematically diagnosing problems to pinpoint the exact cause of a malfunction. Once identified, root cause analysis (RCA) delves deeper to uncover the fundamental reasons behind the issue, rather than just addressing its symptoms. This approach prevents recurrence and enhances equipment reliability.
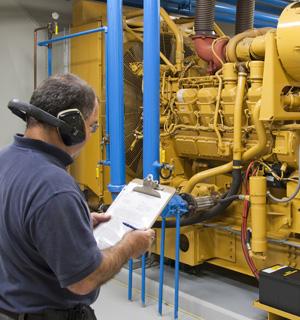
Root Cause Analysis
Engineering consultants use various RCA tools, such as the 5 Whys, Fishbone Diagrams, and Failure Modes and Effects Analysis (FMEA), to systematically analyze and solve problems. These methods provide a structured way to identify potential failure points and implement corrective actions.

Award Winning Firm

Professional Workers

Licence & Insured
Benefits of Equipment Troubleshooting and Root Cause Analysis
These benefits collectively contribute to a more effective and sustainable maintenance strategy.